The company was originally founded in Bergen, Norway during the early 1900s as an engineering blacksmith serving the marine and agricultural industries. After developing the specialisation in stainless steel the business was relocated to England in 1978. At this point in time, Petersen offered a standard range of stainless steel fittings and shackles for marine and industrial uses. Through specialising in the turning, upsetting and forming of stainless steel bar, we began to manufacture a wide variety of products to customer specification for use in other industries.
Throughout the 1980s the company focused on product development. Supplying stainless steel wire terminals enabled Petersen Stainless Rigging to expand both market and manufacturing capability. The strategy proved to be very successful and consequently prompted the company to move to a large modern manufacturing facility at Blaydon-on-Tyne in 1988.
With a design team focused on finding solutions to problems, product innovation has always formed a strong part of development at Petersen: the Shake-Proof Shackle incorporating the smart-lock pin, the Shackle Toggle for wide chain-plates, the failsafe Hi-MOD backstay insulator, the easy-fit Hi-MOD swageless terminal and more recently the slim-line and lightweight GT turnbuckle body were all developed after many hours of customer consultation.
The stainless steel hardware business has been a challenging one over the past 20 years as a whole new economics of production and consumption has radically changed the global market. Petersen has steadfastly refused to join the race to the bottom and instead we have invested heavily in quality programs, staff training and production systems to ensure we win the race to the top. We operate an ISO 9001 compliant quality system which also meets the much more stringent aerospace industry standard AS 9100. Material certificates and certificates of conformity are always available on request (even after goods have shipped). In the unlikely event we discover a problem with a batch of material, we can tell you exactly which invoice it was shipped on to minimise the disruption to your business and your customers.
Our dedication to quality goes far beyond the physical parts we produce. We set targets for and monitor response times to enquiries, on-time deliveries, shipments right-first-time and many other measures to ensure we always give the best possible service.
Petersen operates out of offices in the UK, Sweden, the Netherlands and Malaysia in order to offer the best possible service to our customers regardless of where they are in the world.
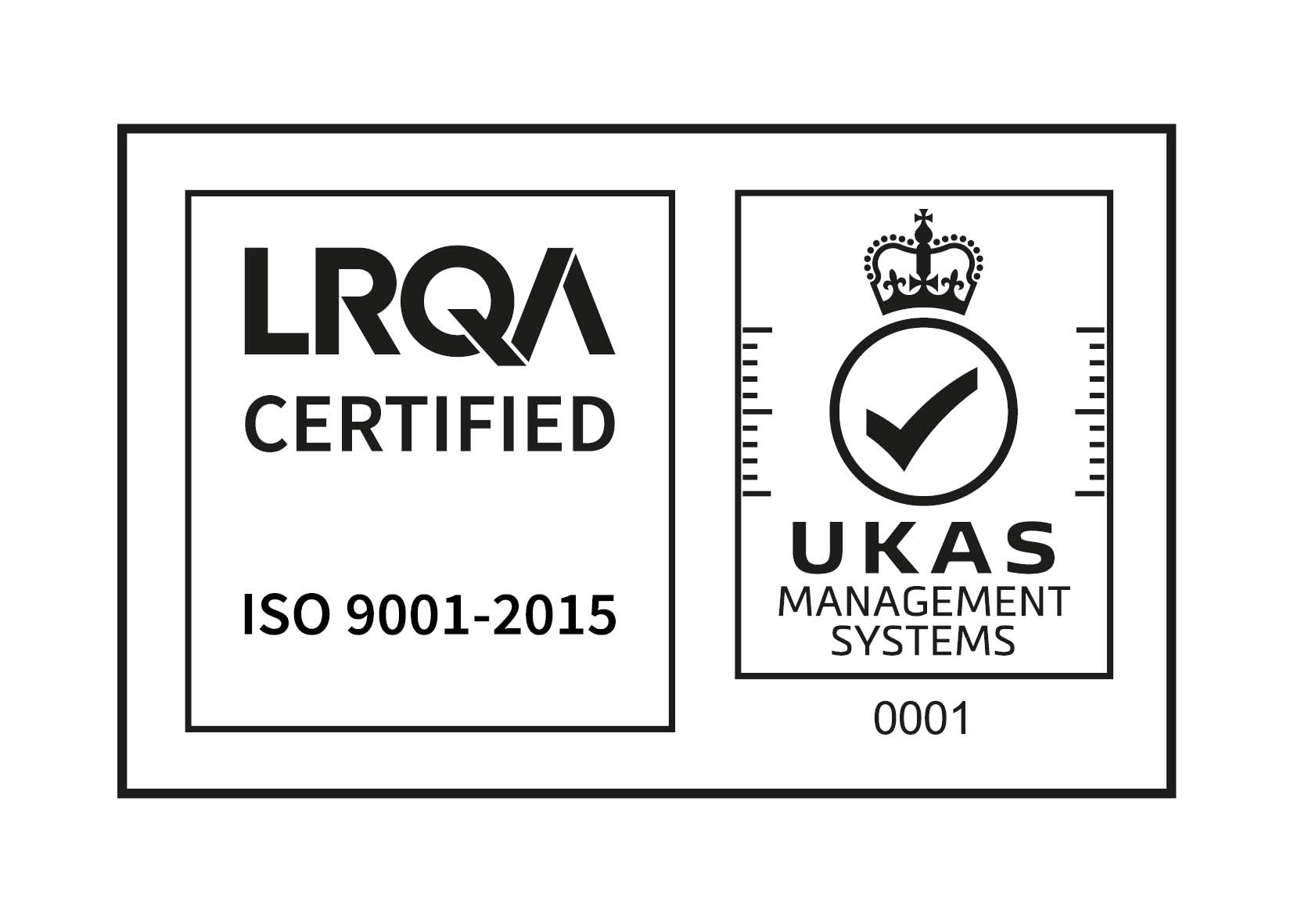