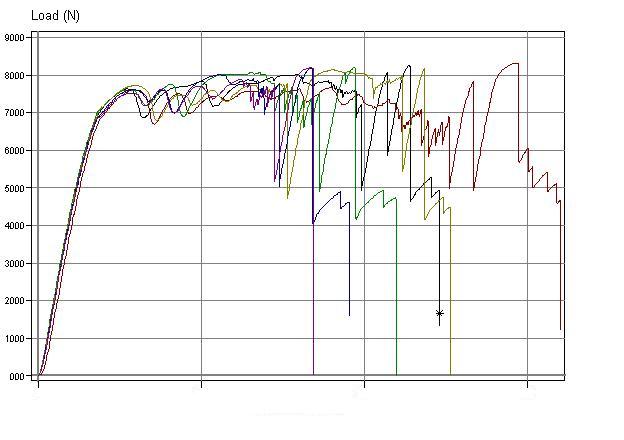
Slip-Stick is the terminology used to describe a phenomenon which can sometimes occur at high loads inside a swage terminal. As the name suggests it is characterised by the wire slipping and then sticking inside the terminal. Other examples of slip-stick are the rubbing of a bow against the string on a violin, the vibration you feel when rubbing a damp finger along a smooth surface (such as the rim of a glass to produce a musical note) the squeal of car breaks or of tyres or train wheels going around a corner or the 'chirrup' of a cricket or cicada.
The graph above shows actual test results from a 3mm 1x19 strand swaged inside a terminal. The load is up the side and the extension (change in length) is along the bottom. The first part of the curve (straight line section) shows the load gradually building to its first peak. We can then see a series of little dips in load followed by peaks. You will notice that the peaks don't get significantly higher even though the extension is increasing. This is evidence of slip-stick. Each little dip represents a slip which is halted by a stick and the load builds again.
A helpful analogy here is towing a car (or boat) with a rope. When first pulling away the tow-rope acts as a spring, storing up energy by extending under load. Once the vehicle you are towing overcomes the initial reluctance to move that energy is released, catapulting the load forward and causing the rope to go slack. The load slows (or even stops if you are not careful) and the rope goes tight again. Eventually the system settles down to a steady state.
In our system the wire-rope is the tow-rope, the mast is doing the towing and the turnbuckle attached to the chain-plate is the thing the mast is trying to tow. Since the turnbuckle can't actually move then the movement must occur inside the swage terminals. Of course in a correctly assembled terminal this would only occur at loads at or above the MBL of the wire-rope (in the test the graph comes from, just above with ultimate failure about 10% over the required MBL). If a terminal is not assembled correctly then there is a chance this could occur at lower loads.
- Ensure the wire-rope is clean and free from oil or grease.
- All Petersen Swage terminals are washed inside and out before leaving the factory. If a terminal has been in your stock for some time take care to check it for dirt and oil and degrease if necessary.
- Ensure your swage dies are maintained correctly and that your after-swage diameter is in tolerance.
- Ensure the wire-rope is fully inserted in the terminal and make full use of the available swage length.
In all tests carried out by Petersen the slip-stick has eventually been halted by cold-welding of the wire to the swage wall (the same process as thread-galling where stainless moves against stainless under load and high friction). However, all tests have been carried out with correctly assembled terminals. At significantly lower loads it isn't immediately clear that the cold-welding process would occur which could result in a wire-rope pulling out of the terminal. It is essential therefore that riggers adhere to the guidance above.